By Lionel Birglen ()
Special thanks to
Prof. Clément Gosselin (Université Laval),
Prof. Yukio Takeda (Tokyo Institute of Technology),
Dr. Klaus Radermacher and Dr. Günter Rau (Helmholtz-Institut),
Prof. Masaru Uchiyama (University of Tohoku),
Prof. Lucy Pao (Colorado University),
and Prof. Yuichi Tsumaki (Hirosaki University)
The basic idea of haptic devices is to provide users with a force
feedback information on the motion and/or force that
they generate. Haptic devices are useful for tasks where visual
information is not sufficient and may induce unacceptable
manipulation errors, for example surgery or teleoperation in
radioactive/chemical environments. The aim of haptic devices is
to provide the user with a feeling of the situation. In this article
we will try to review a particular type of haptic devices, namely
those based on parallel mechanisms.
Introduction Why Using Parallel Mechanisms?
Recent haptic devices are becoming more and more sophisticated and
include several innovative features. To give the user a precise
feeling of the end-effector slave manipulator situation, the haptic
device should be able to generate a wide range of dynamic behavior.
As proposed by Millman and Colgate*, some important features for
high-performance haptic devices should be highlighted: low inertia,
high stiffness, low friction, backdriveability, near-zero backlash,
gravitationnal counterbalancing, sizeable workspace, multiple
degrees-of-freedom, and human matched force capabilities. In addition,
compactness is highly desirable. It can be seen that parallel mechanisms
are appropriate candidates for haptic devices since they are well-known
for their high stiffness and low inertia, which enables large bandwidth
transmission of forces. Other desired properties can be achieved through
suitable mechanical design and proper control scheme. A particular stress
must be put on the transparency of the device regarding the user; the
haptic device must not distort the reflected forces/torques by its
mechanical characteristics.
In this article, we present a brief overview of the most representative
haptic devices based on parallel mechanisms. However, many existent desings
have been omitted for reasons of lacking or redundant information. If you
consider that we are missing something important, feel free to
to provide us with adequate information. Items referred in the bibliography
are indicated by a "*" sign. Links to related web sites can be found either
directly in the text as hyperlinks, or at the end of the present article.
Review of Standard Mechanisms
It is difficult to control parallel mechanisms in real-time,
as required with haptics, because the forward kinematics
is highly nonlinear and is often not in closed form. Moreover, the
gravitationnal counterbalancing required for the hand controller
to appear transparent to the user, leads to software-operated
static balancing, which is increasing the complexity and the
time consumption of the control scheme. To overcome these
difficulties, fast hardware capabilities are required. Alternatively,
extra sensors can be used. Because of the increasing power (computing
frequency) of commercially available computers, controlling a parallel
mechanism with efficient refresh rates can now be achieved.
Medical robotics is of course, an aera of predilection for high-performance
haptic devices. They can provide the surgeon with tremor-free movements by
down-scaling the force applied, and the physical therapist with reliable
rehabilitation system. An European project, the
, an acronym standing for Compact Robot for Image Guided
Orthopedic Surgery, is basically a Gough-Stewart platform aimed at providing
the surgeon with a high-performance tool for bone surgery that is both a
manipulator and a haptic device. Gough-Stewart platforms are also used by the
CAIP in Rutgers University to create an
for domestic use. Besides medical applications,
the Gough-Stewart platform has also been successfully marketed by
AEA Technology as the
to control nuclear robots, and the
University of Colorado as a general
for large multi-dimensional volumes of data.
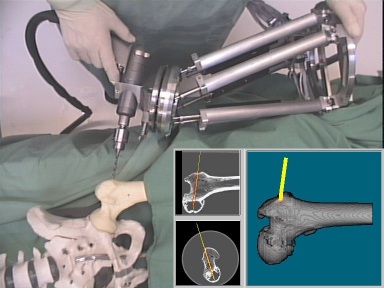
Testing the CRIGOS Robot (courtesy of K. Radermacher and G. Rau, Helmholtz-Institut Aachen, Germany)
Another possible design involves spherical mechanisms. They
present the particularity of having a fixed center point that
can be chosen at the center of the user hand, thus, eliminating
the need for arm motion. Moreover, particular designs can provide
unlimited rotation around this central point, allowing very large
workspace, limited only by the low-scaled dexterity and mechanical
interferences. Such a device has been successfully tested at
Laval University, named the
*.
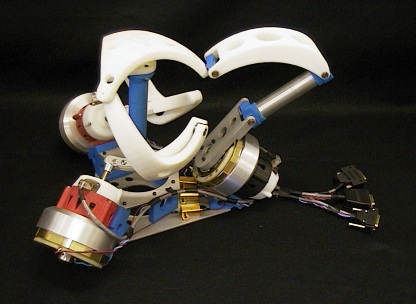
The 3-DOF Spherical Haptic Device, SHaDe (courtesy of Prof. Gosselin, Laval University, Canada)
The latter is a 3-DOF spherical mechanism and has an optimized
workspace with a very high average dexterity and a non-null
minimal dexterity, i.e., no singular configurations at all.
A spherical mechanism has also been used by the
* at Tohoku University as a complementary
subsystem of a modified Delta positionning mechanism, leading to a
hybrid design with high performance: large workspace, low inertia, and compactness.
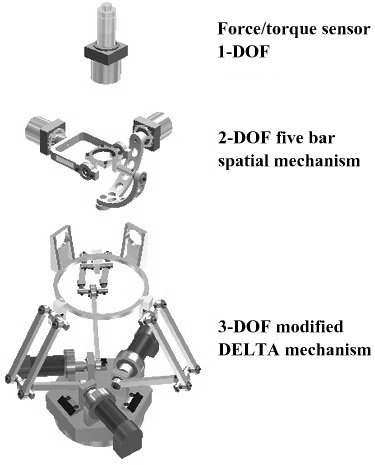
The SML Haptic Device (courtesy of Prof. Uchiyama and Prof. Tsumaki)
The Delta from
can be used as an haptic interface by itself, as the one commercialized by
. A new 6-DOF version has just been released
on the market. An ideal mechanism would have constant
performances all over its workspace, a property known as isotropy.
Unfortunately, typical mechanisms do not present this asset.
Nevertheless, an optimized design based on the maximization of
criteria such as the dexterity can improve the overall behaviour
of the system in a dramatic way. The useable workspace must be,
as usual, free of singular configurations, leading once more to
a careful analysis and optimization of the design. An interesting
method to obtain a singular-free workspace can be achieved by
actuator redundancy as used by Reboulet* at
, and Buttolo at
.
Other designs for the legs of the platform can be used, instead of
previously described systems.
The of Dr. Iwata Lab is a haptic device for desktop use
(fingertip manipulation) based on three pantograph legs, particular
emphasis has been put on reducing the inertia of the system, leading
to a high-bandwidth device. Pantograph designs can also be used for
small and reduced DOF haptic devices, as proposed by McGill University
as a
.
The Robotics Lab at KAIST uses three five-bars linkages in lieu of
classical prismatic links to create their
.
A
with reduced DOFs and linear motors is also investigated in the
Mechatronics and Control Lab at Korea University. Recently,
a 6-DOF parallel haptic device has been designed at Hanyang University.
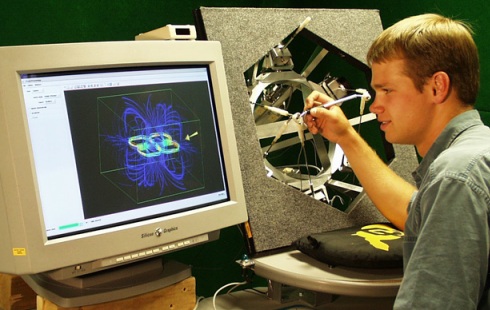
Colorado University Haptic Device
(courtesy of Prof. Pao, Colorado University, USA)
Review of Wire Actuated Mechanisms
Cable mechanisms present interesting advantages in comparison
with conventional parallel mechanisms: their workspaces are
usually much larger and due to the lightweight of cables
inertias are almost null. Hence, fast motions can be achieved
through a wired system. However, two main drawbacks have
considerably slowed the expansion of the use of wired mechanisms.
First, cables can only produce forces in one direction complicating
the analysis of the usable workspace, and second, the latter
unidirectional constraint implies that in order to fully control
the mechanism, actuator redundancy must be employed. Nevertheless,
during the last few years, those difficulties have been overcome and
successful systems have been created such as Falcon,
or
robots.
For a haptic device, a very interesting architecture has been created in the
consisting of
a 6-DOF platform with cables/tendons transmission. What makes this design
particularly original is that it has been extremely well studied using
actuator redundancy, kinematic optimization, and maximized controllable
workspace. Again in Italy, the LAR-DEIS laboratory in Bologna
proposed a finger-operated haptic device, the
(VIDET), with 3-DOFs, completed by a visual
acquisition system and carried as a backpack. Tokyo University has
developped a
with 6-DOFs using only 7 wires with
high force transmissibility and large practical workspace.
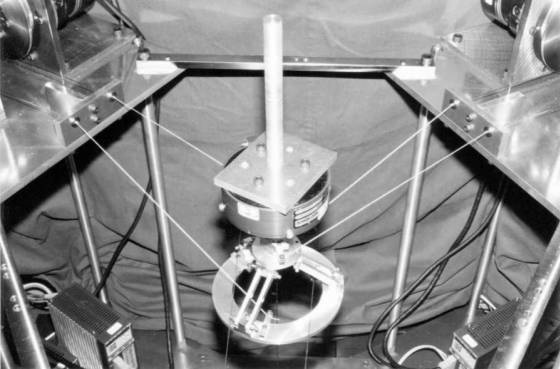
Tokyo University Wire Haptic Interface (courtesy of Prof. Takeda, Tokyo Institute of Technology, Japan)
The BioRobotics Lab of Washington University proposed a wide range
of simple
with steel cable transmission. Despite
the large inertia due to the mechanical design and heavy moving masses,
they keep as a main advantage, a very large workspace.
A Word About Force Control
It was in the late 40's that Raymond C. Goertz* working with the
of the U.S. Atomic Energy Commission, invented the first
master-slave manipulator. Publicly demonstrated in 1949, it was
intended to manipulate radioactive substances. This manipulator was based
on a serial architecture but yet, the haptic sensation was transmitted
to the master arm through parallel mechanism linkages. Later, in the 50's,
Goertz was again the first to implement force reflection for manipulators
using servo-motor systems. Medical applications followed soon in the next decade
when Rotschild and Mann developed a force-feedback artificial elbow for
amputees. But, until recently, the computing power of electronic systems was
too small, or shall we say "too slow", to carry on the calculations in a safe
manner, causing these systems to become unstable. To overcome this problem
Daniel E. Whitney* presented in 1978 the Remote Compliant Center or
RCC a mechanical system based on a parallel architecture to provide
fast and reliable assembly with passive compliance.
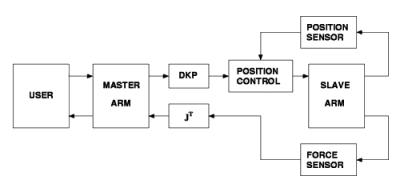
The Remote Compliant Center and a Master-Slave Manipulator Control Scheme
Active compliance or impedance control was then presented by
Neville Hogan* in a concise and rigorous approach in 1985, to provide more
flexibility for assembly robots. The basic idea is to elaborate a control
law that gives the end-effector a certain impedance (usually mass-spring-damper)
by proper command on the actuators. Credits for impedance control should however
be shared with R. Paul, B. Shimano, and J.K. Salisbury. In the past two decades,
research on force control has grown in an exponential fashion with two main
streams of applications. Firstly, there is the affordable way to enhance robotic
system abilities by giving them a supplementary sense, the sense of touch.
And secondly, there is the possibility to provide users with the same feeling
using a mechanical device, then called a haptic device. Researches about force
control are still very active to provide fast and reliable algorithms. Readers
willing to study that subject in detail may found an interesting summary in the
recent book Robot Force Control* from
and
.
. . .
Conclusion
Parallel mechanisms have shown their accuracy with many successful
applications throughout the world as haptic devices. Their stiffness and
low inertia make them appropriate to this end. Since haptic systems are used
by a human operator who has a limited range of movements, the disadvantage
of small workspace of parallel mechanisms is no longer essential.
The Moore evolution of computer systems has now almost overcome
the last drawback of parallel mechanisms their complicated input-ouput
relationships, and hence, their computationally intensive control. Many
different designs have produced successful systems and impressive capabilities
in comparison with classical haptic devices such as the well-known
Phantom™ manufactured by
and shall certainly continue their expansion through the market.
Bibliography
 |
Goertz, R. C., "Fundamentals of General-Purpose Remote Manipulators," Nucleonics, Vol. 10, No. 11, pp. 36-42, 1952. |
 |
Hogan, N., "Impedance Control: An Approach to Manipulation, Part I-II-III," ASME Journal of Dynamic Systems, Measurement, and Control, Vol. 107, March 1985. |
 |
Whitney, D. E., and Nevins, J. L., "Computer-Controlled Assembly," Scientific American, Vol. 238, No. 2, pp. 62-74, February 1978. |
 |
Birglen, L., Gosselin, C. M., Pouliot, N., Monsarrat, B., Laliberté T., "SHaDe, A New 3-DOF Haptic Device," IEEE Transaction on Robotics and Automation, pp. 166-175, Vol. 18, No. 2, April 2002. |
 |
Millman, P. A., Colgate, J. E., "Design of a Four Degree-of-freedom Force Reflecting Manipulandum with a Specified Force/Torque Workspace," Proceedings of the 1991 IEEE ICRA, Sacramento, CA, April 1991. |
 |
Reboulet, C., Leguay, S., "The Interest of Redundancy for the Design of a Spherical Parallel Manipulator," Recent Advances on Research Kinematics, pp. 369-378, Kluwer Academic Publishers, 1996. |
 |
Tsumaki, Y., Naruse, H., Nenchev, D. N., Uchiyama, M., "Design of a Compact 6-DOF Haptic Interface," Proceedings of the 1998 IEEE ICRA, Leuven, Belgium, May 1998. |
 |
Siciliano, B., Villani, L., Robot Force Control, Kluwer Academic Publishers, 1999.
 |
 |
Lee, C. D., Lawrence, D. A., and Pao, L. Y., "A High-Bandwidth Force-Controlled Haptic Interface," Proceedings of the ASME Dynamic Systems and Control Division, DSC-Vol. 69-2, pp. 1299-1308, Int. Mech. Engr. Cong. & Exp., Orlando, FL, November 2000. |
Summary of Related Links
 |
,
A New 3-DOF Spherical Parallel Mechanism for Haptic Interface. |
 |
,
Compact Robot for Image Guided Orthopedic Surgery. |
 |
,
Mechanical Design and Kinematic Optimization of a Novel 6-DOF Parallel Mechanism. |
 |
,
Commercial Version of the Delta-based Haptic Device. |
 |
,
Home of the Haptic-Master. |
 |
,
Gough-Stewart Platform used for haptic purposes. |
 |
,
About The Pen Based Force Display, for Micro-Manipulation. |
 |
,
Haptic device for perception of large multi-dimensional volumes of data. |
 |
,
Cable Actuated 3-DOF Haptic Interface. |
 |
,
Spatial In-Parallel Wire-Driven Mechanism with Six Degrees of Freedom. |
|