By Luc Rolland
It is in the middle 90's, in the footsteps of the Delta robot success, Mr. Clavel asked Mr. Rolland to investigate
new parallel robot designs in order to achieve displacements with three translations and one or two useful rotations.
The designs had to be applicable to industry as low-cost material handling manipulators. The specification criteria were
very high throughput and simple construction. If possible, the design had to find innovative means to increase workspace,
somewhat limited in parallel manipulators. Mr. Rolland came up with the idea to focus on one rotation at first, thus on
4 DOF manipulators, and proposed the Manta architecture. This robot is 4 DOF quadrapod also using the parallel-bar
principle in order to eliminate rotations.
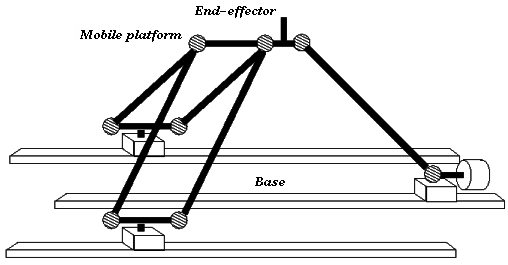
Schematic of the linear Manta robot
The Design
The Manta manipulator features three main kinematics chains. It allows displacements along three translations and
one rotation which is the sideway tilting of the mobile platfiorm.
The basic idea behind the Manta robot design is not far from that behind the Delta robot design since it is again
making use of parallelograms. A single parallelogram chain cannot restrain any rotation but the conjunction of two
chains allows to block two rotations, of which one is along the end-effector axis that is perpendicular to the mobile
platform. Each parallel bar is maintained together by two stiff springs. The third kinematics chain is made of one
single bar along which platform rotation is transmitted.
In order to increase workspace, the manipulator structure is making use of linear axes which include the actuators and
sensors. They can either be in a parallel or perpendicular layout. But any other linear actuator layout can also lead to
significant configurations. These actuators can be linear motors, linear motion guides, etc. The parallel axis layout
brings the unlimited workspace potential which can be used in warehouses, for example. The main linear actuator
disadvantage is acceleration which is somewhat limited by technology since the commercially available axes are limited
to 5 G.
The use of three base-mounted actuators and low-mass links allows the mobile platform to achieve accelerations of up
to 5 G in experimental environments. These figures could be better if stiffer structures were built or linear motors used.
The mobile platform has been built with passive paltform joints which are very concentrated in order to keep the structure
as stiff as possible by respecting the triangular transeversal configuration made by the facing parallel bars.
This makes the Manta robot a perfect candidate for high-throughput pick and place operations for such applications as
media (CD, DVD, cassette) changer in a mediatheque, material handling in heavy payload conditions and wharehousing.
The use of base-mounted actuators and low-mass links allows the mobile platform to achieve accelerations of up to 5 G's
in experimental environments. This could be further improved if stiffer structures are built or linear motors are used.
The mobile platform has been built with passive paltform joints, concentrated in order to keep the structure as stiff
as possible by respecting the triangular transeversal configuration made by the facing parallel bars. Inasmuch, the
mobile platform has to have the two single bars to be located as far apart as possible so that smaller forces may be
used to maintain platform position.
The performance of the Kanuk robot makes it a perfect candidate for high-throughput pick and place operations for applications
such as media (CD, DVD, cassette) changer, material handling in heavy payload conditions and wharehouse operations.
The First Prototype
A prototype of the Manta robot has been constructed at EPFL.
Bibliography
 |
Clavel, R., "Conception d'un robot parallèle
rapide à 4 degrés de liberté," Ph.D. Thesis, EPFL, Lausanne, Switzerland, 1991. |
 |
Rolland, L., "The Manta and the Kanuk: Novel 4-DOF Parallel Mechanisms for Industrial Handling,"
Proc. ASME Dynamic Systems and Control Division, IMECE'99 Conference, Vol. 67, pp. 831-844, Nashville, USA, Nov. 14-19, 1999. |
Related Links
|