By Professor Georg Michael Pohl
The HANDLEX was created during an internal research project of the University of
Applied Sciences FH Bochum (Germany) somewhere around July 2000. The project
was carried out by an elektical engineer and myself in partnership with a nearby
company designing linear actuators (PAV - Antriebstechnik). Two students in
mechatronics worked on the design and fabrication of the robot as part of their
theses.
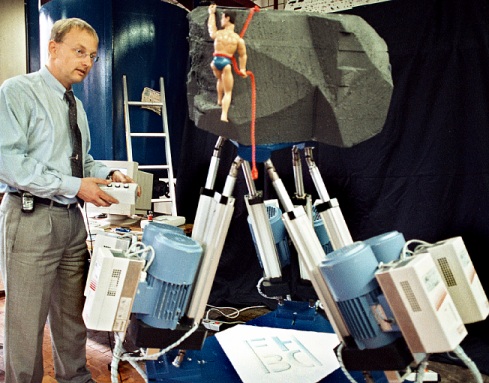
The HANDLEX parallel robot during demonstration
The Design
The main topic of the little research projekt was to solve the control problem of
a hexapod structure and on the other hand to realize this with a very low budget
(German universities of applied sciences have the tenth of the budget of other
universities). Our goal was to show our competence in mechatronic design.
The following were the principal tools and components used to build HANDLEX:
- standard three-phase motors with brakes;
- electrical remote cylinder / ball roll spindle;
- KEB performance static frequency changer;
- the block-oriented simulation language WINFACT-BORIS
() for the control
of the six frequency converted AC-motors (not servo drives!);
- 6 incremental encoders to reach the necessary accuracy;
- a Pentium 133 MHz PC motherboard with ISA and PCI;
- cheap Taiwanese measurement boards
();
- MS Windows 3.11.
Based on the above, we reached a performance accurate enough for positioning a
in three axes with a 0.3 mm precision a working piece which has to be manipulated
by a second robot carrying the tool. The motion speed is too low for hydro pulse
testing applications because of the cheaper version of the frequency converters
and, of course, because of the inefficient 0.5 KW AC-motor.
The following are the characteristics of HANDLEX:
| Linear drive stroke: | 310 mm; |
| Axis travels in X, Y, Z: | 300, 300, 300 mm; |
| Range of tilt angle: | ±30°; |
| Max. rates of travel in X, Y, Z: | 1000 mm/s each; |
| Max. accuracy: | ±0.5 mm; |
| Load capacity: | 300 kg (6 x 1500 N); |
| Drive power: | 3.3 KW (220 V phase connection). |
We hope to find applications, where the costs are more important than the speed or
the accuracy. The total cost of the robot, excluding assembly cost, was about 12,000
Euro, or some 10,600 USD. Particularly, the robot can be used as a motion simulation
or a welding jig carrier.
Bibliography
 |
Djajakusuma, R. "Konstruktion eines elektromechanischen Hexapode Gelenkroboters",
Diploma Thesis, FH Bochum, Germany, August 30, 2001. |
 |
Stridde, W., "Digitale Regelung eines elektrospindelgetriebenen Hexapode-Sitzes",
Diploma Thesis, FH Bochum, Germany, December 24, 2001. |
Related Links
|